CEO report
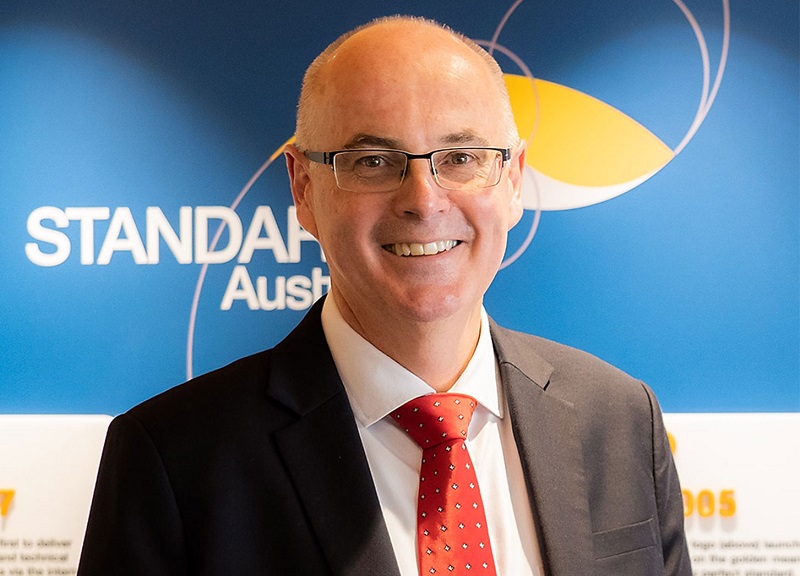
We had planned to host our annual Standards Awards dinner in Melbourne to celebrate the achievements of this year’s and last year’s recipients. Unfortunately, with COVID-19 in circulation, we had to cancel at the last moment. But the lack of an in-person ceremony doesn't diminish our appreciation, and I want to acknowledge the dedication shown by our deserving winners.
This type of dedication, through the commitment of time and knowledge, is essential to the work we do. The Standards Awards are a celebration of the important role that contributors play in the standards development process. My thanks go to the more than 5,000 contributors for their ongoing commitment.
Our NEXTgen program supports volunteers at the beginning of their careers, with young professionals provided with exciting opportunities to become involved in national and international standardisation. The NEXTgen 2020–21 participants graduated this month and, despite the inability to celebrate in person, their accomplishments were celebrated with an online ceremony.
Lastly, the inaugural Mid-Year Member Meeting took place on Friday 28 May. The agenda included the good order of the organisation, an update on its strategic direction, and an opportunity to discuss matters of significance in relation to both national and international standards development.
— Adrian O'Connell, Chief Executive
Standards Awards Winners 2021
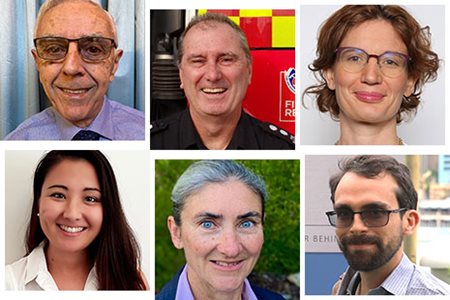
The annual Standards Awards recognises excellence in standards development. We acknowledge those who champion change across their industry, make a positive impact and are committed to the continual development of standards. The recipients of this year’s awards are of an exceptional calibre.
Congratulations to the 2021 winners (pictured in order below):
- W.R Hebblewhite Medal – Alan Whittle
- Meritorious Contribution Award (National) – Mark Porter
- Meritorious Contribution Award (International) – Aurelie Jacquet
- Emerging Leader Award – Taru Veijalainen
- Emerging Leader Award – Cath Chalmers
- Emerging Leader Award – Peter Kilby
- Outstanding Committee Award – SF-054, Safe Design of Livestock Ramps and Forcing Yards
Learn more about the winners on our awards page.
Developing standards for a sustainable future
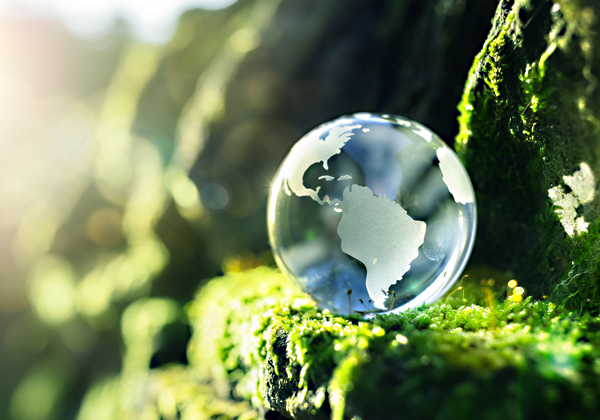
As an organisation, we recognise the importance of emissions reductions standards that support the Commonwealth’s climate change commitment to the 2015 Paris Agreement. The Carbon Dioxide Capture, Transportation and Geological Storage (CCS) Project, that recently kicked off, will develop a Technical Specification for the storage and handling of liquefied and gaseous hydrogen.
Read more in our recent media release.
Practical guidance for record management software
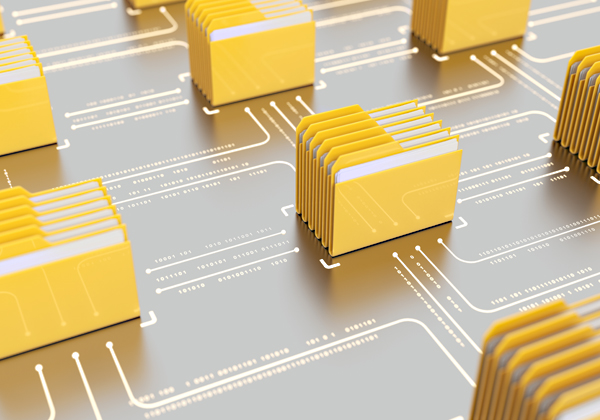
With digital recordkeeping becoming more essential to businesses of all kinds, implementing sound record management principles is of ever-increasing importance.
Standards Australia has recently adopted revised international standard AS/NZS ISO 16175.1, and Technical Specification SA/SNZ ISO TS 16175.2. They provide guidance to organisations on the integration of digital recordkeeping practices so that records remain accessible even as technology advances.
Read more in our media release.
Building Commissioning Technical Specification
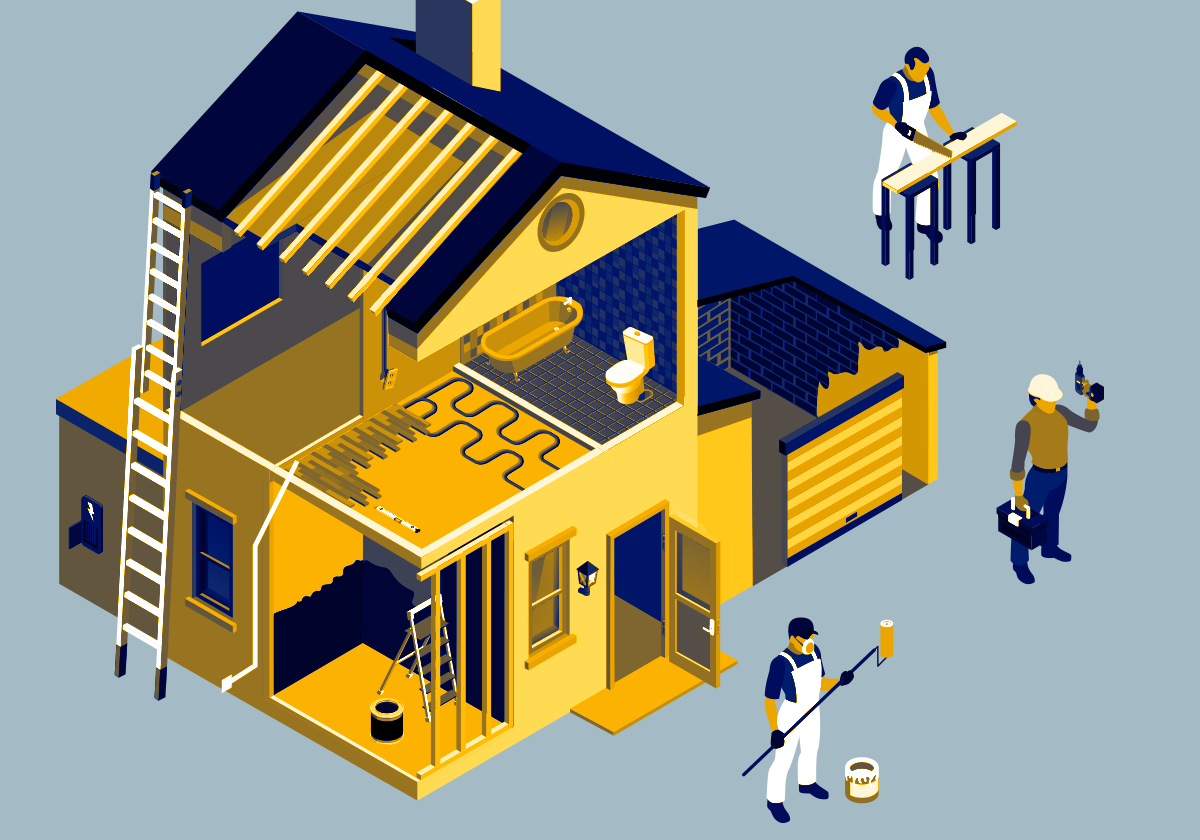
Standards Australia has recently published SA TS 5342:2021, Building Commissioning, a Technical Specification aimed to support industry by improving consistency, awareness and outcomes of the building commissioning process.
Read more in our recent media release.
Strong digital strategies help IT governance
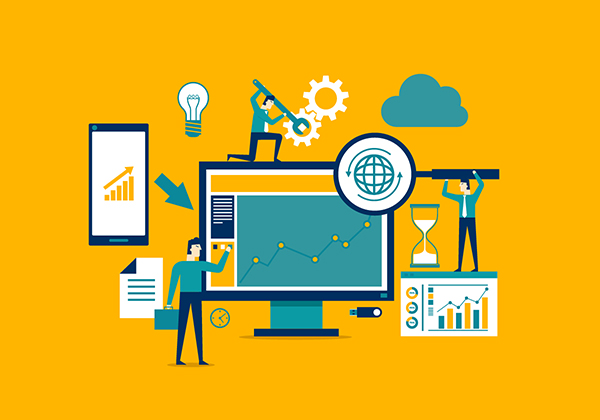
The challenges of 2020 demonstrated that businesses with strong digital strategies can not only survive, but flourish. Yet with technology evolving so quickly, how can business leaders know they are making the best choices for their organisations now and in the future?
Standards Australia recently spoke with Jan Begg, Chair of ISO/IEC JTC 1/SC 40, IT service management and IT governance. In addition to her role as Chair to the joint international committee, Ms Begg is also the Chair of Australia’s mirror committee, IT-030, ICT Governance and Management, which has played a key role in developing standards in this area for many decades.
Read about the development in governance of IT in our recent article.
Raising the standard for future leaders
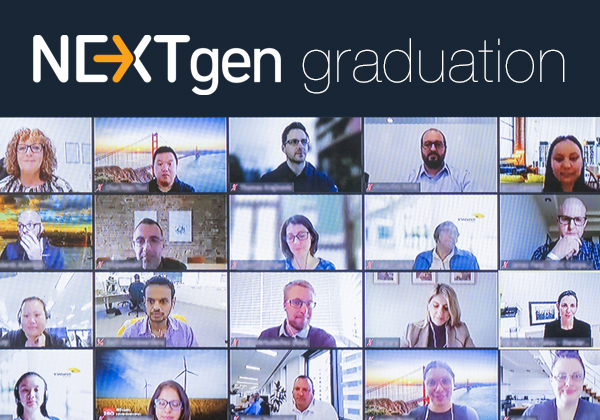
Standards Australia hosted the NEXTgen program’s 2020–21 graduation ceremony on 6 May, with participants joining online from across Australia to celebrate their achievements. This exciting program educates emerging leaders on the impact standards have in Australia. Three recent graduates reflected on their experiences participating in the program in a recent article.
Applications for the 2021–22 program are open. To take advantage of this opportunity, visit the NEXTgen page.
IEC Young Professionals Programme
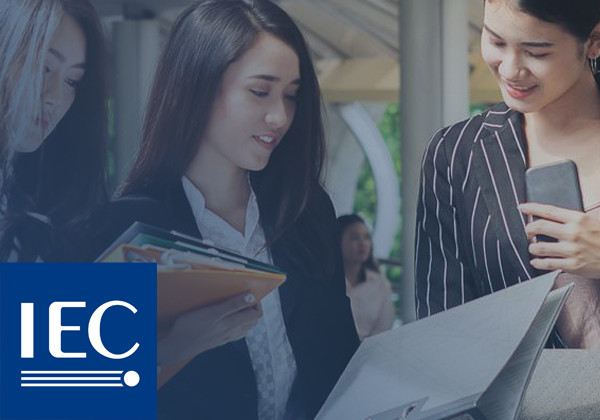
The International Electrotechnical Commission announced that they are accepting applications for the IEC Young Professionals Programme for 2021, with the opportunity for remote participation by Australian applicants. Participants will have the opportunity to see the IEC in action and meet technical experts from all over the world. This is an excellent way for young professionals to boost their international profile.
ISO & IEC consultation survey
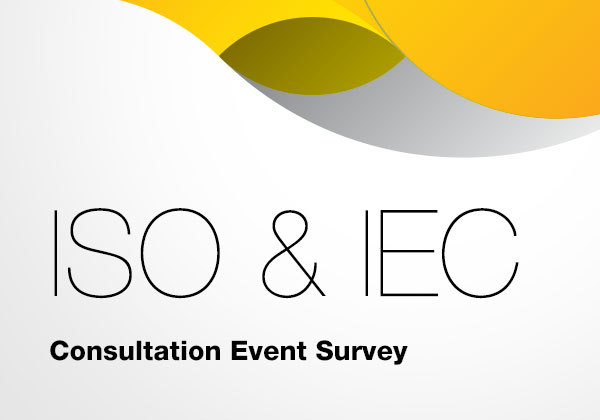
Recently, a consultation session was held on ISO and IEC participation, which saw 177 contributors join to learn about Australia’s presence and current priorities across international governance groups.
We are keen to collect feedback to better understand the Australian experience in the international system. All ISO or IEC contributors are invited to complete the survey by 15 June 2021.
SDAC communique May 2021
The Standards Development & Accreditation Committee (SDAC) is a Committee of the Standards Australia Board. The committee assists us to fulfill our responsibilities as Australia’s peak national standards body, and meets regularly to discuss the wide range of matters relating to standards development and accreditation work.
Often unseen, SDAC has been referred to by many as the engine room of Standards Australia, powering our contributors to get things done. Since October 2020, a Communique of SDAC meetings is being made available to stakeholders. The goal is to provide a direct insight into the discussions and recommendations of the committee and reflects our commitment to lead with transparency and include stakeholders in our processes.
You can access the May 2021 SDAC communique (PDF) and further details on SDAC and its members on our website.
In Conversation with Alex Kingsbury
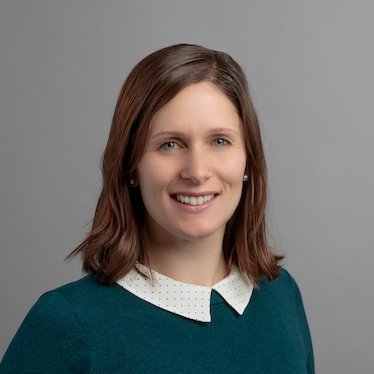
Alex Kingsbury has worked in the development of metal technologies, including additive manufacturing and metal powers for the last ten years. Ms Kingsbury is currently the independent expert on ME-028, Additive Manufacturing, and is an Additive Manufacturing Industry Fellow at RMIT University where she leads Engagement for the RMIT Centre for Additive Manufacturing.
Standards Australia (SA): When did you first become involved in standards development?
Alex Kingsbury (AK): In 2018, I received a call regarding the possibility of starting an Additive Manufacturing committee in Australia. I’ve been involved from the start, as I was asked to participate as an independent expert on the committee and I also suggested other people I knew to form the committee.
SA: How do standards impact and interact with your industry?
AK: Standards have a big impact in our industry. 3D printing is still a new field, so the quicker we can develop and deliver standards, the more standardised and reliable we become as an industry. A number of people across the world are involved in standards development for 3D printing, so it is very much a global effort. People in the industry would love for us to move quicker, as there is a compelling need for standards. It’s interesting the way that standards have the ability to reduce costs, by streamlining supply chains, and making our contracting process clear and transparent. The other aspect is we have standards that we can rely on from the market verticals that we feed into, and also adjacent fields. Take for example, aerospace standards for manufacturing, biomedical standards, and also standards around material testing and characterisation. We have been fortunate enough to be able to rely on some of these standards while we go about creating 3D printing specific standards.
SA: Why are accessible standards important?
AK: In addition to the above, I think it’s important that we’re all speaking the same language, and have a common guidebook for how to build, specify, test, measure, and control our processes and parts. Without standards, there is a lot of room for confusion and error. Standards also offer an unbiased, and non-commercially controlled view of 3D printing. This is very important as in the earlier days, when standards were less mature, bigger companies tended to really dictate the terms of any 3D printing transaction. With standards in place, smaller companies have more chance of being competitive. With more companies competing on an even playing field, we get better results for end-users, and ultimately, more acceptance of 3D printing technologies.
SA: What is the future of standardisation in your area of work?
AK: We need more industry-specific standards, for example, a standard on how to clean a 3D printed mesh on a medical implant. We also need standards committees to constantly review the field and emerging trends and respond in a measured, but also in tune way. Currently some types of 3D printing technologies aren’t recognised as 3D printing, yet the industry does recognise them. I also suspect we will see standards being constantly updated. It feels like at the moment the minute a standard is released, there are already new modifications waiting for the next version. Our industry is very globalised, so I think we’ll continue to see it trend that way, with more countries participating in the joint working groups and contributing to standards development.
International update
Standards Australia represents Australia on the two major international standards development bodies, the International Organization for Standardization (ISO) and the International Electrotechnical Commission (IEC). Our activities are reported on our International Updates page.
Highlights from May (PDF)
- Updated guidance for developing International Standards
- Guidelines for the promotion and implementation of gender equality: New Work Item Proposal
- Rollout of revised IEC Copyright Policy
Sector update
Access the latest standards development news in your industry sector via our Sectors page.
Drafts open for comment
The public comment process provides an opportunity for stakeholders and members of the public to make valuable contributions. With the launch of our new public comment platform, draft standards currently open for comment are now available via Connect.